Danone, one of the world leaders in four different businesses – essential dairy and plant-based products, early life nutrition, medical nutrition, and waters – has been striving since 1919 to build a unique health-focused portfolio of goods. In 2017, the French Group invested in the development of an avant-garde production plant in Parets, Spain. The food multinational chose E80 Group to integrate and automatize all the intralogistics operations of the new plant, from the management and warehousing of raw & packaging materials up to the end-of-line and shipping.
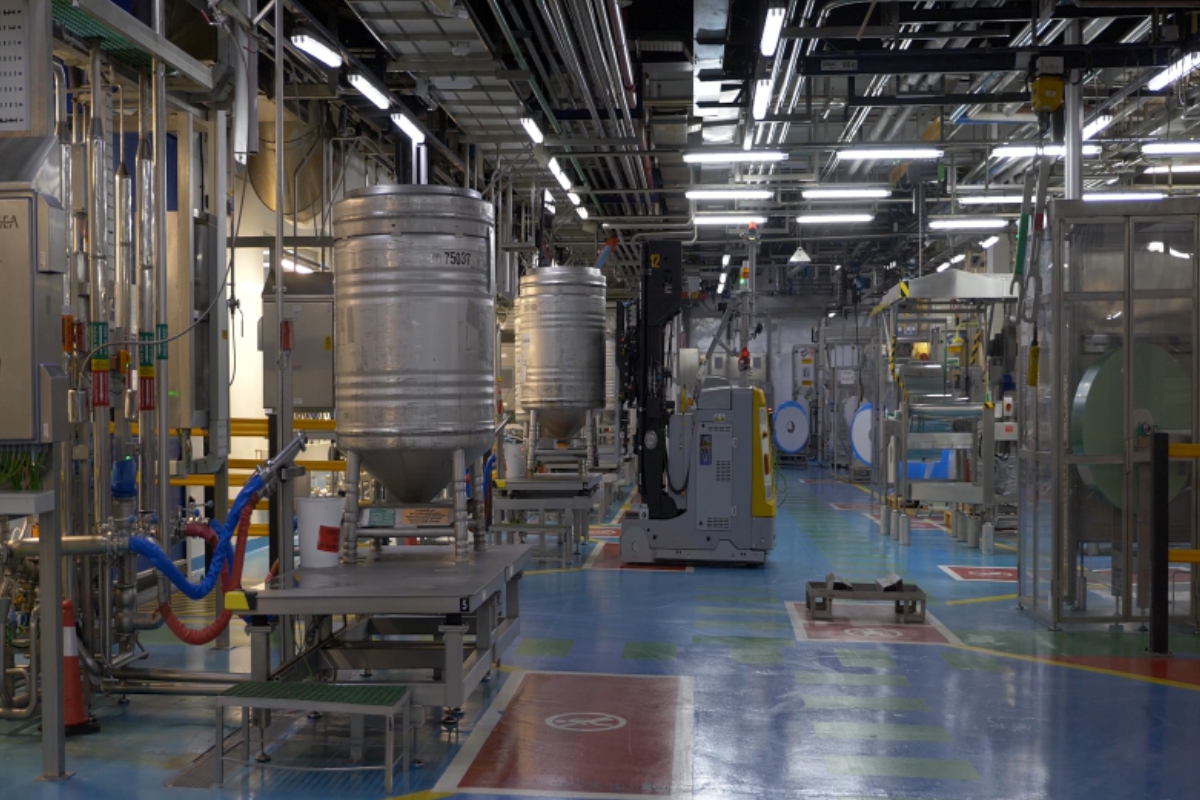
A few kilometers from Barcelona, its hometown, the 51,000 m2 facility becomes the first Danone center in Europe to develop, along with dairy products, plant-based alternatives to coconut-based, and oat-based yogurt, enhancing the adoption of healthy, sustainable, and inclusive eating and hydration habits.
Here are the goals to be achieved with this factory digitalization:
- To get complete traceability not only of all the materials managed and handled within the facility but also of all the flows carried out throughout the day
- To control and minimize costs related to loss of raw material turnover
- To optimize the performance of the warehouses according to FIFO and FEFO inventory schemes
- To improve the safety levels of the operations
- To eliminate any production downtime
The E80 Group team addressed these challenges by providing Danone with a complete ecosystem of solutions, totally coordinated and supervised by SM.I.LE80, the Smart Integrated Logistics software platform.
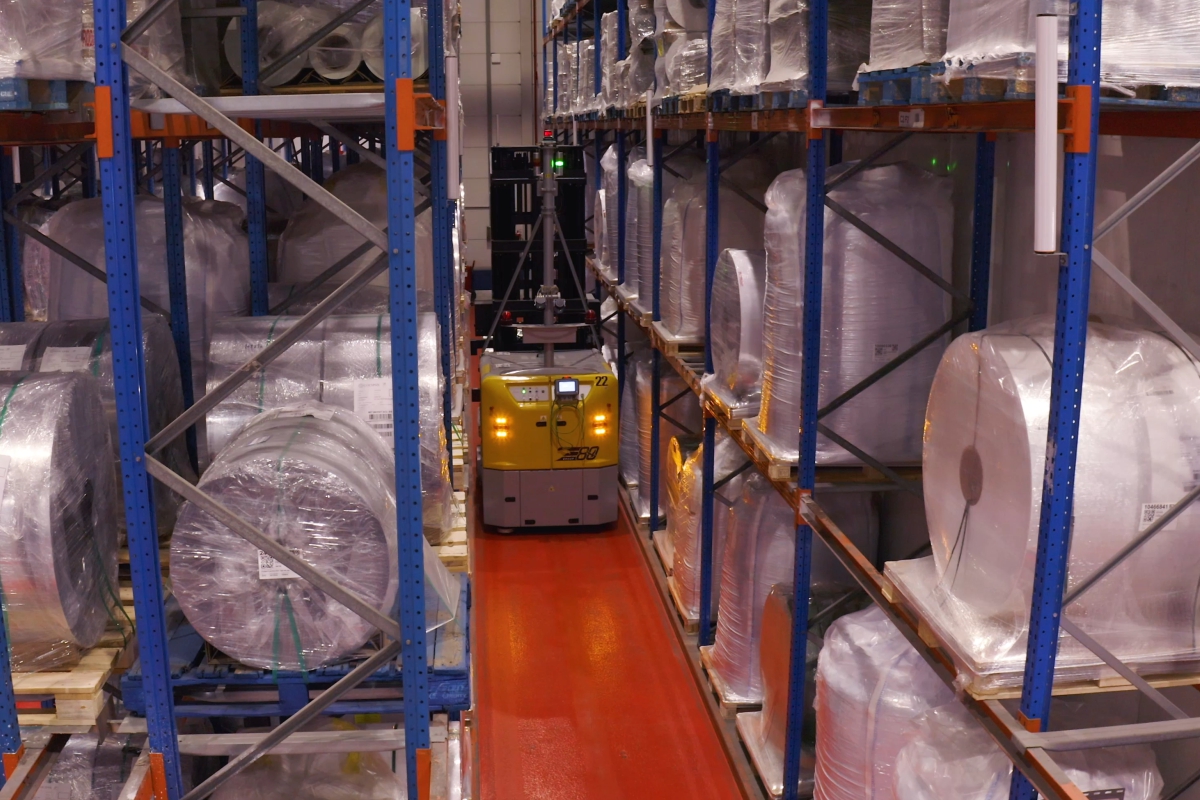
THE ADDED VALUE OF THIS PROJECT
“For the Danone team it has been fundamental to dialogue with only one partner,” Javier Casassas, Industrial Projects Technician at Danone Group, says. “Otherwise, the greater the number of interlocutors, the greater the loss of efficiency of a system. It is an innate, essential condition. The supplier must be competitive in software, hardware, and efficient solutions to meet the industrial customer’s needs, which implies great flexibility”. Flexibility and partnership that E80 can guarantee to Danone’s team 24/7, 365 days a year, with its digital customer service which is always ready to promptly address any need.
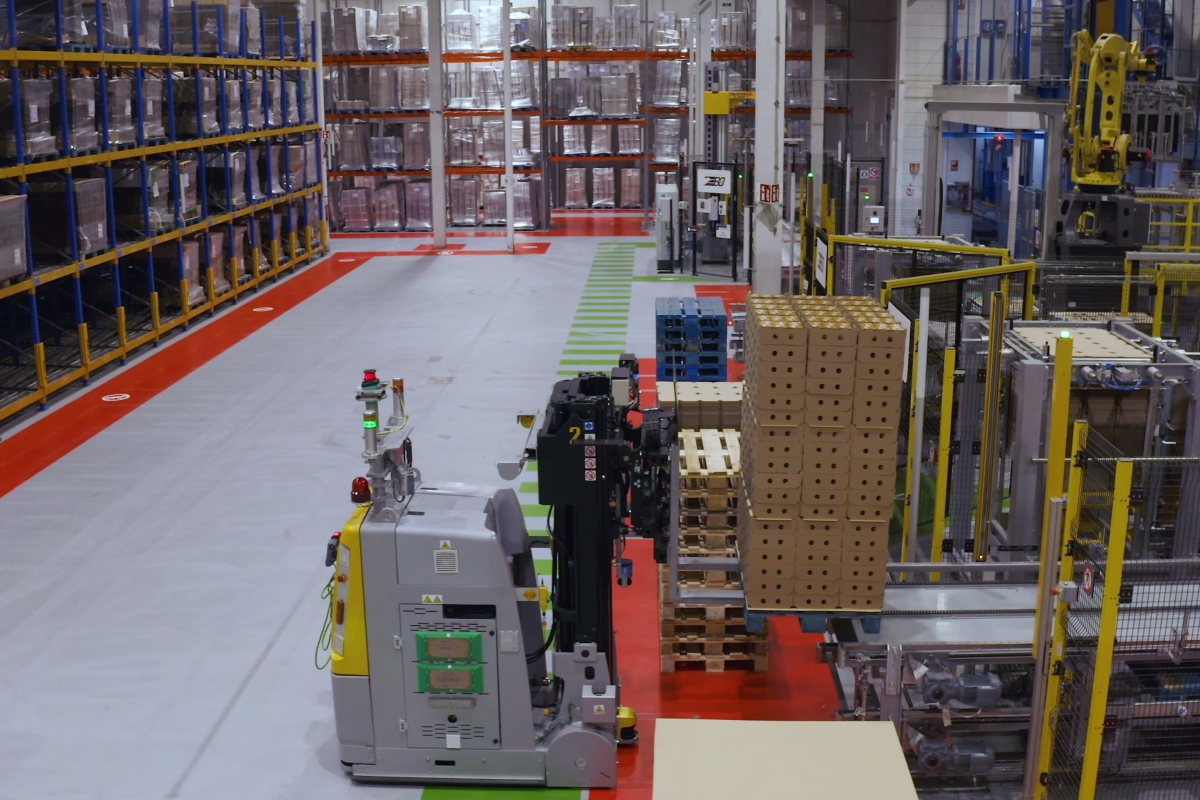
This business success story represents a great example of tight synergy between E80’s team and its customer on the common path to develop a safe, sustainable, and efficient Smart Factory.
Watch the video: