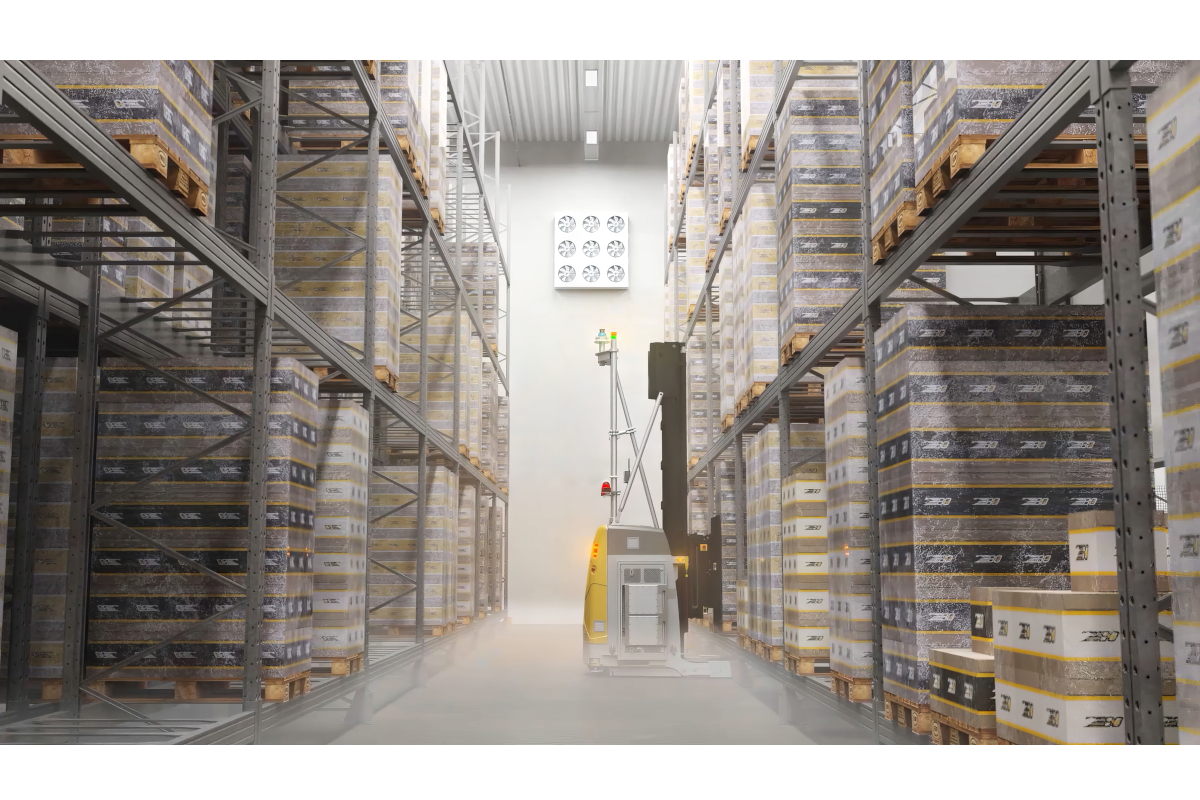
In the ever-evolving cold chain ecosystem, the pursuit of logistics and warehousing high performance has emerged as a paramount goal for businesses aiming to maintain a competitive edge. A groundbreaking solution that’s transforming the industry is the combination of automated guided vehicles and high-bay warehouses. This game-changing synergy offers several advantages, fundamentally reshaping the storage, retrieval, and transportation of goods.
INTRALOGISTICS: THE KEY TO OPTIMAL OPERATIONS
Within an industry for which it is vital to ensure food quality and efficient operations, intralogistics plays a key role in enabling the optimization of handling, storage, picking, and shipping at the required temperatures. Manufacturers and distributors, driven by market dynamics, are encountering a series of challenges. These encompass the pressing need for higher productivity to meet surging market demands, the necessity for quicker stock turnover, and the ever-expanding array of products falling within the temperature range of -4°C to -26°C.
In this transformative landscape, the cold chain’s rulebook is being rewritten by the joined use of automated guided vehicles and high-bay warehouses. Efficiency, precision, and adaptability are the cornerstones of this revolution, promising to change the very essence of how we store, retrieve, and transport goods in the pursuit of optimal cold chain operations.
REVOLUTIONIZING COLD CHAIN THANKS TO E80 GROUP’S SOLUTIONS
Also developed to respond in a scalable and flexible way to the performance needs of the cold chain, the solutions of E80 Group, an Italian-based multinational specialized in integrated and automated solutions for manufacturers and distribution centers, primarily in the food, beverage, and tissue sectors have been revolutionizing the way deep-freeze warehouses operate. Also with its Smart Integrated Logistics (SM.I.LE80) software platform, which manages all intra-logistics flows, and laser-guided vehicles (LGVs) portfolio, the Group offers flexibility to its customers while significantly increasing plant efficiency and product traceability throughout the supply chain.
In order to guarantee the most efficient intra-logistics solution, E80 Group provides consulting and after-sales services, such as discrete-event simulation software and 24/7 remote and on-site support. The SmartDesigner plays a key role in the design phase, as tests are carried out in a simulated and controlled environment. This makes it possible to obtain results before the implementation, as well as to establish investments and apply the required modifications. All the current and future operating scenarios are assessed, thus enabling the development of a realistic scenario. This allows to maximize process optimization in plants where many variables are in play, verify flows, identify potentially critical issues well in advance, and validate the most appropriate control logics with 95% reliability.
Moreover, the Group offers a vast array of after-sales services aimed at protecting the added value guaranteed by the implemented solutions over time and meeting the demands that may arise during the lifecycle of the system, such as new market situations and different production requirements.
With a focus on innovation and sustainability, this integrated strategy aims to guarantee safety in warehouses and to ensure a smooth and efficient workflow in deep freeze plants, where the extreme environment creates difficult working conditions for personnel.
The purpose is to optimize productivity and service to customers while maintaining the quality and integrity of temperature-sensitive goods.
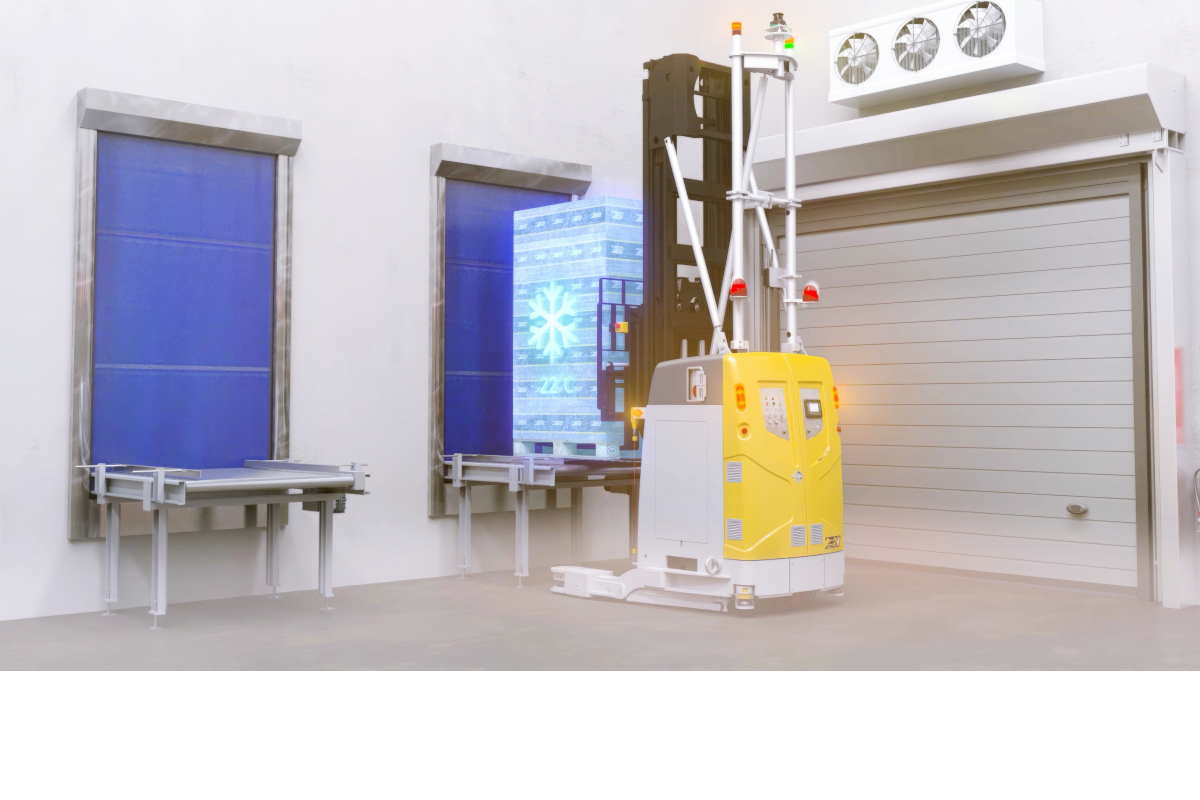
LGVS’ AND AUTOMATED WAREHOUSE PERFORMANCES IN SUB-FREEZING PLANTS
The use of LGVs connected with different types of storage, engineered to operate even in temperature conditions as low as -26°C, has been crucial in deep-freeze manufacturing and distribution operations.
In detail, E80 Group laser-guided vehicles interact seamlessly with various systems bringing the right product in the right place at the right time. All LGVs designed for deep freeze environments feature internal heating systems, insulated and thermoregulated hydraulic power units, and lithium batteries enabling operations in temperatures as cold as -30°.
One of the most important automated storage solutions for industries requiring cold storage is the use of advanced AS/RS systems for the automated handling of products in several different storage layouts, ensuring high performance, reliability, and energy efficiency even under freezing conditions. The integration with LGVs makes the entire solution completely flexible and each crane completely independent, eliminating the risk of bottlenecks. In this scenario, one of the keys to optimizing performance and reducing cost per pallet is to maximize density while ensuring the required throughput rate. The complete solution is designed to be modular and upgradeable.
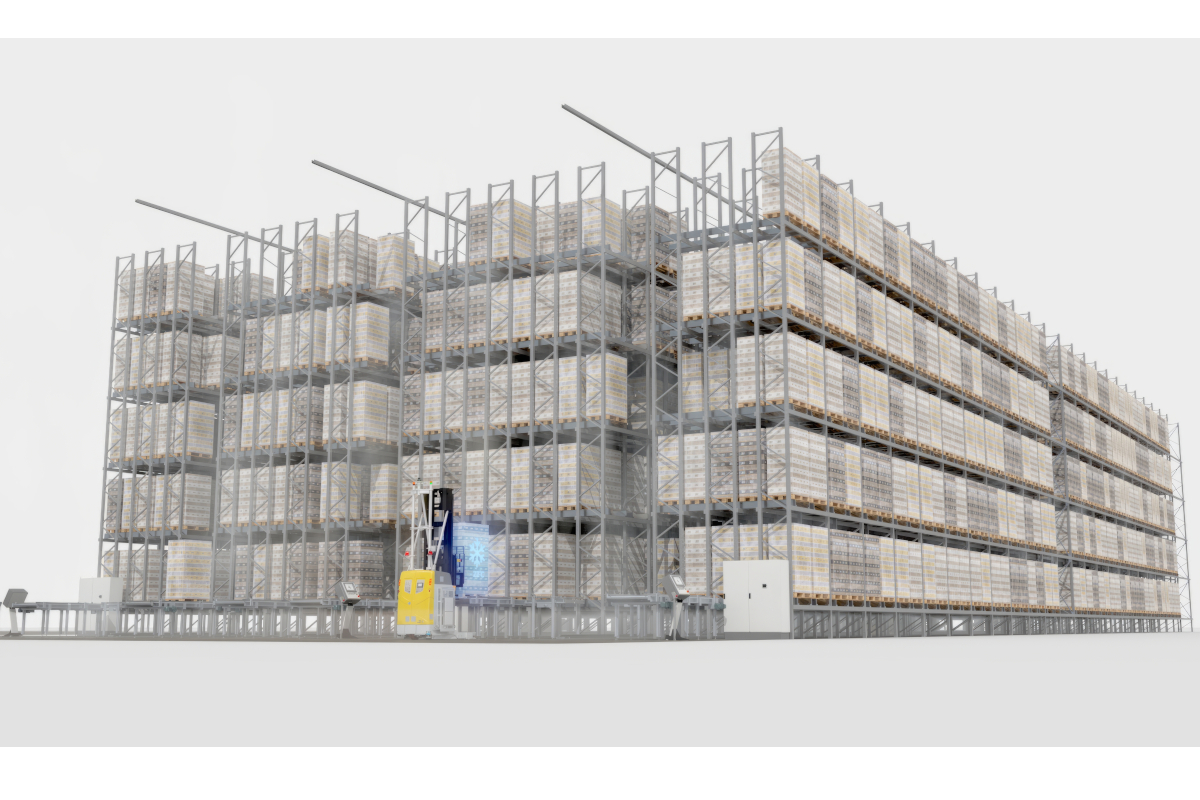
By combining Smart Integrated Logistics software, E80 Group empowers manufacturers and distribution centers to meet the challenges of deep freeze environments head-on. These technologies not only optimize operations but also preserve product quality, and ensure traceability, and safety throughout the supply chain, ultimately benefiting both businesses and their consumers.
To take a closer look at how these customizable and configurable solutions can have a pivotal role within deep-freeze warehouses, let’s see an example of one of E80 Group’s customer plants handling and storing frozen foods.